
for lead production
Electrowinning processes
for lead production
The FLUBOR Process – Patented system for the hydrometallurgical recovery of lead from Galena-based concentrates
The unique features of the FLUBOR Process include:
- Direct leaching of Pb concentrate with no pre-treatment
- Production of Pb and S
- Elimination of slag production and SO2 emissions
- Environmental impact reduction to the minimum values
- Limited fuel consumption
- Improved workplace environment
The FLUBOR Process uses a chemical stable fluoboric acid based electrolyte as solvent for Pb. The process is composed by the following units:
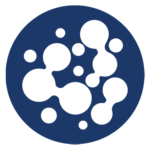
Leaching
the leaching of the PbS concentrate is accomplished in an acidic oxidising solution where the Galena mineral is contacted with a solution containing fluoboric acid and ferric fluoborate. The sulphur of the galena is oxidised to elemental sulphur while lead is taken in solution as lead fluoborate. This leaching is higly selective with metals more noble than Pb reporting to the leaching residue.
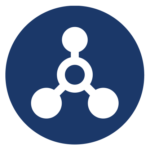
Electrowinning
the solution from the leaching unit is then sent to a diaphragm divided electrowinning cell. The Pb is plated in the cathodic compartment while the iron is oxidized in the anodic compartment to regenerate the leaching solution. This unique electrowinning cell allows the Flubor process to operate as a closed loop leach and EW system.
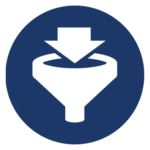
Bleed treatment
although highly selective, the leaching of mineral concentrates allows some impurities into the solution. These impurities can eventually affect downstream processes and also consume free fluoboric acid in the solution. The bleed treatment it is based on the precipitation of metal sulphates less noble than lead. In this unit impurities consuming fluoboric acid are removed from the process and the free acid is recovered to the process.
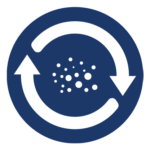
Residue treatment
sulphur contained as elemental S° can be removed and recovered allowing the metal values contained in the remaining residue to be recovered using existing processes. Engitec has developed a patented technology that is able to directly treat the Flubor leach residue without prior S° removal.
- The Lead extraction rate is > 97 %
- The produced lead cathodes have a Pb content of 99.99 % free of Bi, Ag, Se, Te.
- The operating cost is exceptionally attractive and substantially lower than the thermal processes used today.
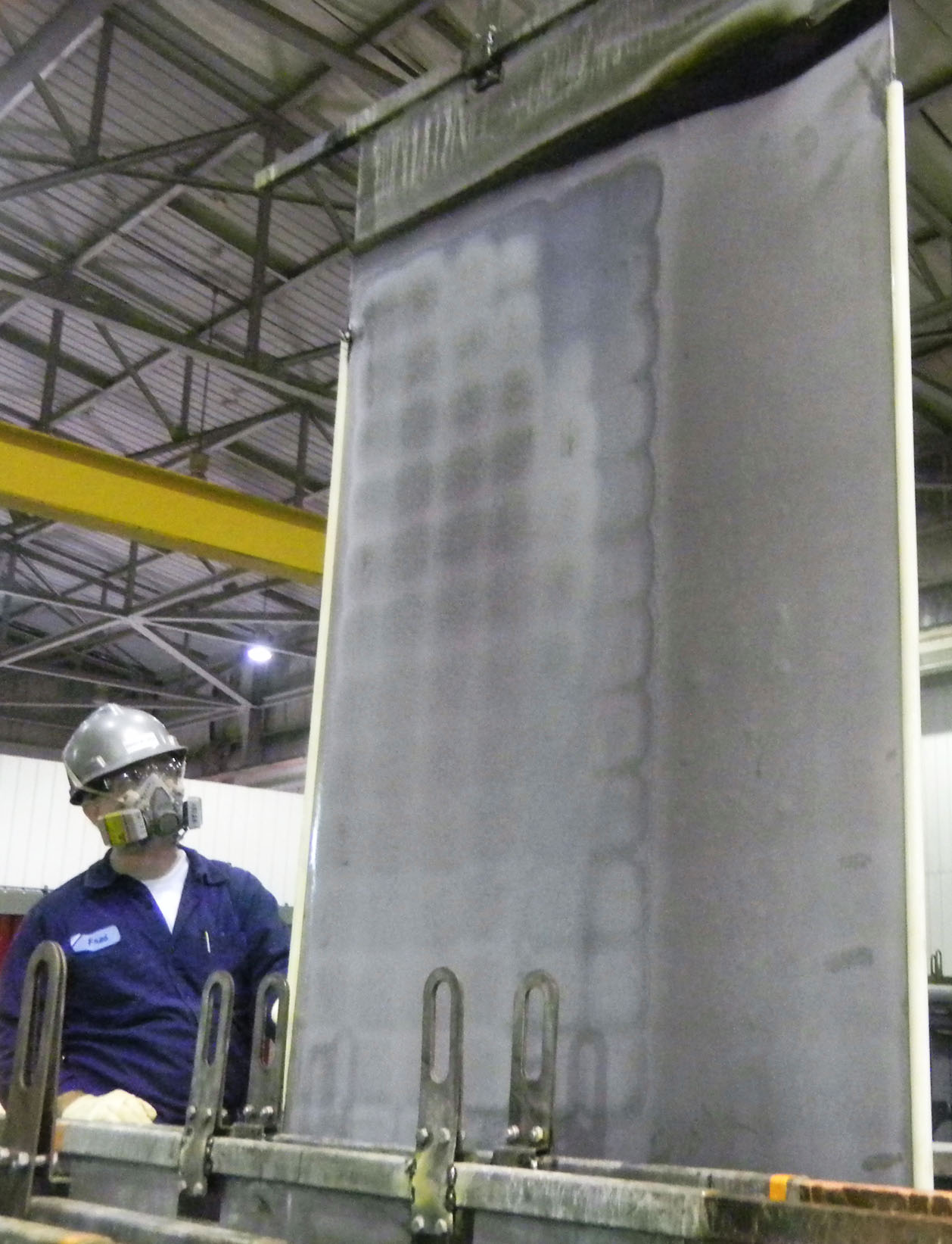
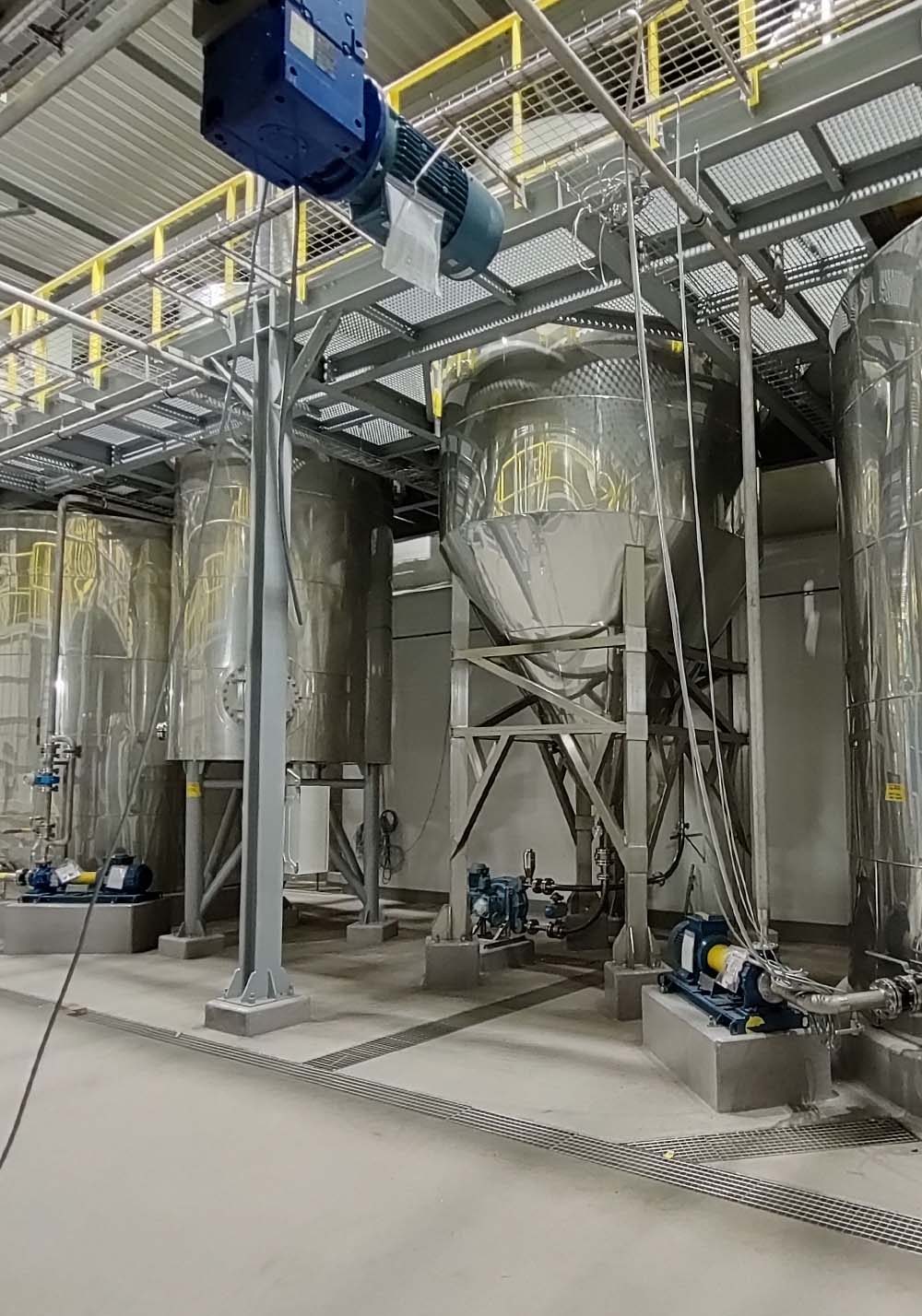
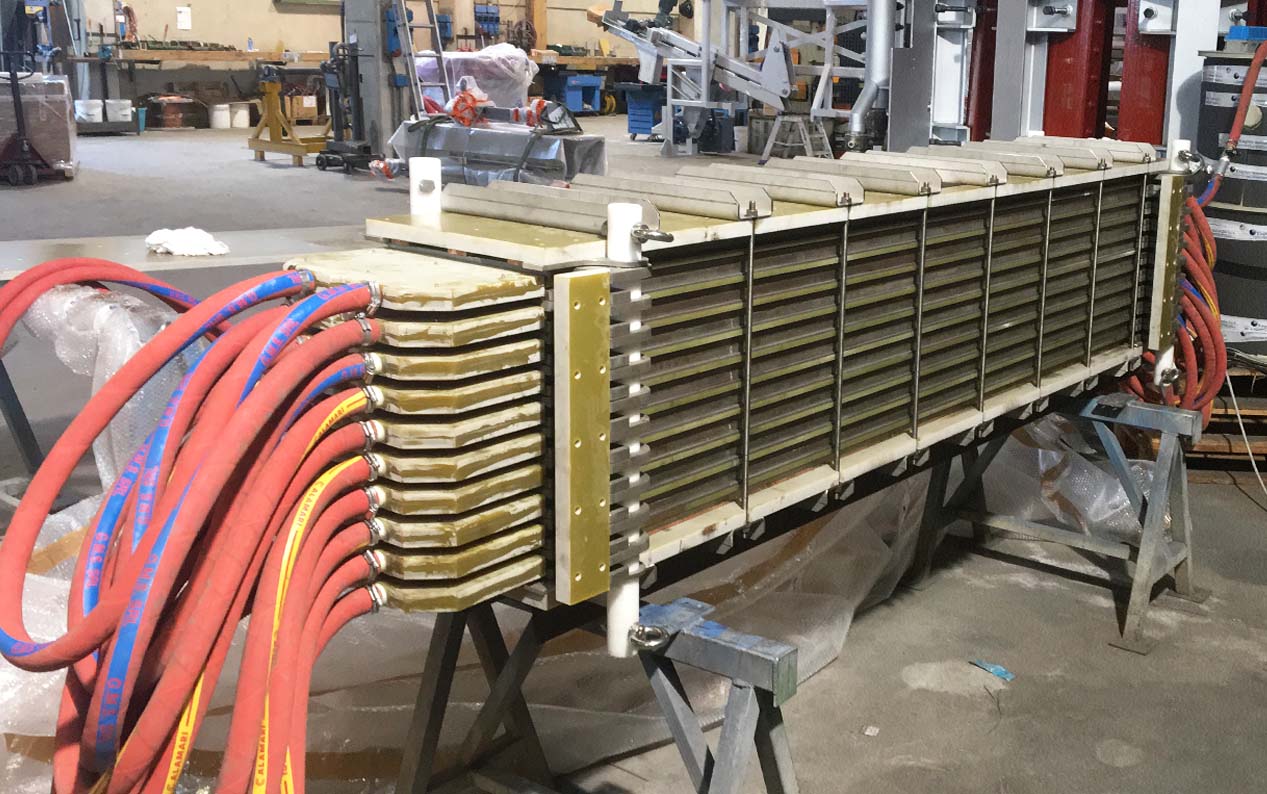

DESCRIPTION OF THE PROCESS
The FAST® Process is a hydrometallurgical/electrochemical system able to produce flakes of metallic lead from an aqueous environment after having leached lead compounds. This means to practically cut the emissions while dramatically reducing the production of solid waste.
No liquid effluents are released. Sulphur is removed as gypsum of quite high quality. The plant, based on a very peculiar electrochemical process, is fully automated and works directly on the paste as produced. The workplace is very comfortable and quite different from a lead smelter.
The FAST® Process is based on 4 steps:
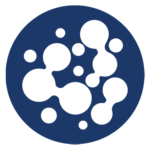
Leaching
The first step is the leaching, where lead contained in the paste is leached in an ammonium chloride-based solution. To leach PbO2 we used till now hydrogen peroxide. Now we have implemented a method that uses the fine coming from the battery breaker. The residue, 5 – 6 % of the feed, contains 5-10 % of Pb and 5 – 10 % of Sb and can be further processed to recover the contained values.

Sulphur removal
The second step is the sulphur removal, where the leached sulphur, present in solution as sulphate, is precipitated as gypsum of good quality.
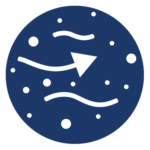
Cementation
The third step is the cementation, where the solution is contacted with metallic lead to remove the metals more noble than lead, as silver and copper, that, otherwise, will be plated decreasing the quality of lead.
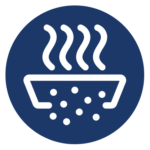
Electrolysis
The fourth step is the electrolysis where, in a flow EW cell, the lead is plated in form of flakes. The flakes are taken out of the cell by the liquid flow and are separated from the water by a screen and then dehydrated by press rollers in form of small flat sheets and fed to the kettle to be melted in a proper industrial shape. The electrolyte is recycled back to the leaching to start another loop.
Pure lead as flakes The quality lead flakes produced by the FAST-Electrowinning Unit can be then processed in the refinery; dross can be recirculated to the process in the leaching unit.
Total Lead (HG standard > 99.9% Metallic Cements
This product is a mix of metals, slightly oxidized, which mainly contains Cu and can be sold to copper producers for the recovery of its components.